What started out as a simple way to monitor our 3D prints turned into a full blown remote control system for our Prusa i3 MK3s! This setup produces stunning timelapses that make the print look like it is rising from the print bed on its own.
So how does it work? One of our lab assistants, Jason Tyler, who spearheaded the project, explains, “It all starts with the Raspberry Pi, which is a mini computer that serves as the brains of the system. This computer is connected to both the printer and the camera that we have watching the prints. It runs a special operating system that connects to our network and has a bunch of special features that makes this project possible.”
In essence, after each layer printed the software talks to the printer and tells it to move the extruder (the big printer head that does the ‘printing’) out of the way, then tells the camera to take a picture. This is done using the GCode language, which is the universal programming language of most 3D printers. When compiled at the end, the pictures are stitched together into a seamless video.
Videos aren’t the only thing that Octoprint can do, Jason says. “The Octopi software allows us to start new prints, monitor current print status, and view prints layer by layer from anywhere!. There is a plugin store where the community has uploaded a bunch of add ons for Octoprint that give this project an extensive amount of possibilities.”
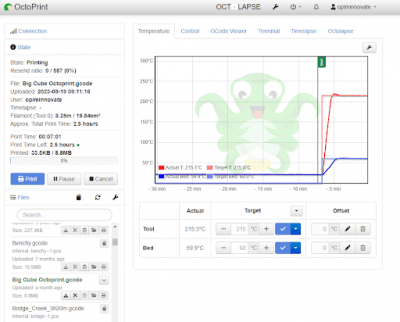
Having a system like this fits in perfectly at OPIM Innovate: It provides a glimpse into some real world skills and projects students might not encounter elsewhere. Octoprint essentially acts as a load/supply management system that increases operational efficiency; similar to examples in the manufacturing industry. Students can view real-time analytics and optimize their print settings from the cloud!
If you are following us on Tiktok or Instagram you may have seen some of these videos before. Come by the lab from 9-4 Monday to Friday to see Octoprint in action!